New to the concepts of inbound and outbound logistics? You’re in the right place.
This guide breaks down the key differences and strategies for both. Learn how optimizing these processes can streamline your supply chain, boost efficiency, and improve customer satisfaction.
TL:DR:
Key Takeaways
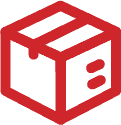
Inbound logistics receives materials from suppliers. Outbound delivers finished products to customers.
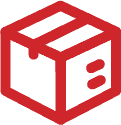
Inbound logistics focuses on supplier selection, purchase order management, and efficient receiving processes.
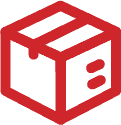
Outbound logistics optimizes order processing, picking, packing, and shipping to ensure timely delivery.
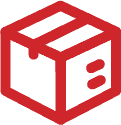
Inbound process: Choose suppliers, place orders, coordinate transport, inspect goods, and manage storage.
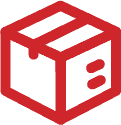
Outbound process: Validate orders, pick and pack products, arrange shipping, and provide customer service.
What are inbound and outbound logistics?
Inbound logistics encompasses all processes involved in receiving raw materials or finished products from suppliers and delivering them to your company’s warehouse, distribution center, or store.
Outbound logistics, on the other hand, deals with the processes that move finished products from your storage facilities to the end customer. This process includes order fulfillment, packaging, shipping, and handling returns.
The combination of these types of logistics makes sure necessary materials and components are available, correctly stored, managed, and delivered without damage and within your promised delivery timeline. These processes are the key to maintaining customer satisfaction.
Key differences between inbound and outbound logistics
The difference between inbound and outbound logistics is their focus and role within the supply chain. Inbound logistics streamlines the supply of goods production or sale requires, while outbound logistics delivers the finished product to the customer.
In inbound logistics, products start at suppliers and manufacturers, move through distributors, and end up at companies that either use them in production or sell them directly.
Outbound logistics, however, is the process of delivering goods from the company to the customer.
Inbound and outbound logistics address different aspects of the supply chain — securing necessary supplies versus meeting customer needs by delivering a product. Each function balances supply and demand, helping a business operate smoothly and efficiently.
Importance of effective inbound and outbound logistics
Streamlined supply chain
When both inbound and outbound logistics are finely tuned, goods move smoothly from suppliers, through the warehouse, and on to customers.
Efficiency in these processes saves considerable time and effort, avoiding unnecessary delays or complications.
Enhanced inventory and order accuracy
A well-organized inbound logistics process receives and stores goods, reducing the likelihood of lost or damaged inventory.
Similarly, a meticulous outbound logistics process, with its focus on order fulfillment and shipping, minimizes errors like mislabeled shipments or incorrect packaging.
Optimized delivery speed
Efficient inbound logistics and outbound logistics allow for faster order processing, from receiving and picking to packing and shipping.
This efficiency enhances customer satisfaction through timely deliveries and gives companies a competitive advantage in the marketplace.
Improved sales and revenue growth
Processing and delivering orders promptly and accurately increases customer satisfaction, which can lead to repeat business and positive word-of-mouth.
Streamlined inbound logistics and outbound logistics can also reduce the cycle time of inventory. More frequent turnover and better cash flow can fund other business operations or expansions.
Reduced operational costs
An effective outbound logistics and inbound logistics process helps reduce overall operational costs. Streamlined inbound logistics processes and outbound logistics processes require less manual intervention, lower the risk of error, and decrease the need for excessive inventory holdings, all of which contribute to reduced labor and storage costs.
Minimizing inventory loss through better inbound logistics and outbound logistics practices also saves on costs from waste and unsellable stock.
Step-by-step inbound and outbound logistics processes
There are several key steps involved in the inbound and outbound logistics processes.
Inbound logistics processes: Receiving
01
Identifying and choosing the right suppliers
The inbound logistics process begins by determining the necessary inventory and finding the best suppliers or manufacturers. Choose partners who can consistently provide the quality and quantity you need, especially for items that need special handling due to their size.
02
Placing and confirming purchase orders
Once you choose a supplier, place a purchase order. Confirm the details of the order, including costs and delivery schedules. Maintain thorough documentation and tracking procedures during this stage to effectively manage the transit of these large items.
03
Coordinating transportation to distribution channels
After confirming the order, ship the goods. The method of transportation — whether by ocean, air, or ground — depends on the size of the items, the urgency of delivery, and cost considerations. Check that the chosen transportation method syncs with your inventory cycle and storage capabilities.
04
Inspecting and documenting upon arrival
When goods arrive, your receiving team will check and document the shipment. They verify that the items they received match the purchase order in type, quality, and quantity, which is particularly important for bulky items that can be challenging to handle and store.
05
Organizing for efficient storage
Move goods to storage areas and organize them so they are easy to access and use. Follow proper storage practices to avoid damage and degradation, which is particularly important for large-scale inventory.
05
Managing reverse logistics
Reverse logistics involves the handling of returns or exchanges. This process is key for maintaining customer satisfaction and inventory accuracy.
Reverse logistics includes:
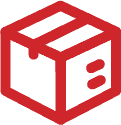
Assessing the condition of returned items
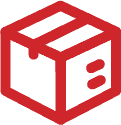
Reintegrating undamaged items into the inventory
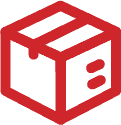
Repairing damaged items where possible
This process increases customer satisfaction by allowing returns and reduces waste by repurposing or repairing products.
Outbound logistics processes (shipping)
01
Validating and processing orders
As soon as a customer places an order with you, outbound logistics processes the order.
The order flows through your business’s order management system, which routes it to the appropriate warehouse or fulfillment center. The fulfillment center adds the order to the fulfillment queue for processing.
02
Picking and packing of products
Once the fulfillment center validates the order, workers pick items from their storage areas and pack them for shipping.
Because large, bulky items are difficult to handle, workers must pay meticulous attention during picking and packing to prevent damage. Safeguard items during these processes to avoid damage during transit.
03
Arranging for transportation
Once the items are securely packed, they are handed off to transportation carriers such as FedEx, UPS, or USPS. The carrier and method of shipping you select generally depends on the item’s size, the urgency of the delivery, and the destination.
04
Customer service and troubleshooting
After the items leave the warehouse, the outbound logistics team will address any customer inquiries or issues that come up.
Effective communication is vital here, especially if there are unexpected delays or complications during shipping. Prompt and transparent communication helps maintain customer satisfaction and manage expectations.
Important logistics key performance indicators (KPIs) to track
Monitor relevant KPIs to gauge the effectiveness of your inbound and outbound logistics operations. These metrics evaluate operational efficiency, identifying areas you can improve and helping align your logistics activities with your overall business goals.
Inbound logistics KPIs
- On-time delivery rate
Measures the percentage of orders suppliers deliver on time, showing you how reliable your supply chain is. - Average lead time
How long it takes to receive a shipment after placing an order. This metric evaluates how well you manage your inventory and how efficient your suppliers are. - Damaged goods rate
The percentage of items you receive that are damaged, which shows you the quality of your transportation and handling processes. - Returns processing efficiency
How quickly your team processes and resolves returns, impacting customer satisfaction and inventory costs. - Freight bill accuracy
Safeguards the accuracy of shipping costs and freight billing. - Loading and unloading times
Measures how efficient your warehouse is at loading and unloading goods.
Outbound logistics KPIs
- Order accuracy rate
Tracks the percentage of orders you deliver without errors. - Average order processing time
The time it takes from receiving an order for your team to dispatch it. - Average delivery time
How long it takes an order to reach its destination after dispatch. - Damaged goods rate
The percentage of orders that arrive damaged, indicating the quality of packaging and handling. - Order volume
Monitors the number of orders processed, which can help in resource allocation and operational planning. - Perfect order rate
The proportion of orders fulfilled perfectly, without any issues throughout the delivery cycle. - Inventory turnover
Assesses how often you sell and replace inventory over a period. - Supply chain costs
Tracks the total costs associated with your supply chain operations, vital for budgeting and financial planning. - Customer order cycle time
The total time taken to complete an order from the point of customer request to delivery. - Cash-to-cash cycle time
Measures the time between spending on supplies and receiving payment from customers, important for cash flow management. - Return rate
The rate at which customers return purchases, affecting inventory levels and reverse logistics.
Four best practices for enhancing your inbound logistics
Follow these four best practices to optimize your inbound logistics process.
01
Evaluate your current operations
Regularly assess the performance of your inbound logistics to identify cost inflators, sources of waste, and areas producing substandard quality. Compare your practices against industry benchmarks and competitors to see how you can improve.
02
Analyze decision-making impact
Evaluate how your purchasing and supplier selection impacts your operations over time. Large purchases might seem economical due to volume discounts, but can cost more in the long run due to excess inventory management. Understand the main cost drivers, such as procurement, transportation, and warehousing, to better manage expenses.
03
Forge strong supplier relationships
Cultivating robust relationships with your suppliers supports a reliable supply chain. Benefits of good supplier relations include competitive pricing, reduced lead times, and enhanced product availability, which are crucial for businesses handling large or specialized items.
04
Use the right warehouse management system (WMS)
To significantly automate and refine your warehouse operations, consider implementing a robust warehouse management system (WMS). If you need a WMS, choose one that aligns with your specific business needs and has capabilities that make handling large, bulky items more efficient.
Four best practices for enhancing your outbound logistics
01
Develop collaborative supply chain networks
Foster collaboration and strengthen ties with essential inbound and outbound logistics partners such as carriers, third-party logistics providers (3PLs), and freight handlers. These strategic relationships optimize inbound logistics and outbound logistics workflows, secure favorable service conditions, shorten delivery cycles, and negotiate cost-effective agreements.
02
Minimize transit times
Refine your transportation methods to minimize delays and cut expenses. To expedite deliveries to customers, consider scheduling carrier pickups more frequently or switch to faster shipping services.
Work together with established 3PLs, as they often have robust relationships with carriers. These connections can help you secure bulk shipping discounts, improve delivery reliability, and enhance overall shipping efficiency. These benefits save on delivery time and shipping costs.
03
Leverage technology for automation
Use technology to automate routine tasks such as order processing, inventory management, and shipping scheduling. Automation increases accuracy and frees up your team to focus on more strategic tasks, enhancing overall productivity.
04
Enhance customer communication
Maintain transparent and proactive communication with customers throughout the delivery process. Use tools that provide real-time order tracking and status updates. Keeping customers informed reduces service inquiries and increases satisfaction.
Elevate your inbound and outbound logistics processes with Red Stag Fulfillment
Efficient inbound and outbound logistics are crucial for ecommerce success, especially when handling large, bulky items. Red Stag Fulfillment specializes in optimizing these processes, offering advanced WMS features, strategic locations, and expertise in large product handling. We streamline your supply chain, reduce costs, and improve customer satisfaction.
Ready to elevate your logistics operations? Start a conversation today.