Warehouse Services
State-of-the-Art Warehousing And Fulfillment
Warehouse services are at the heart of your eCommerce business. Ensure your products are stored properly and strategically with a warehousing and fulfillment provider that treats your products like their own.
Let’s talk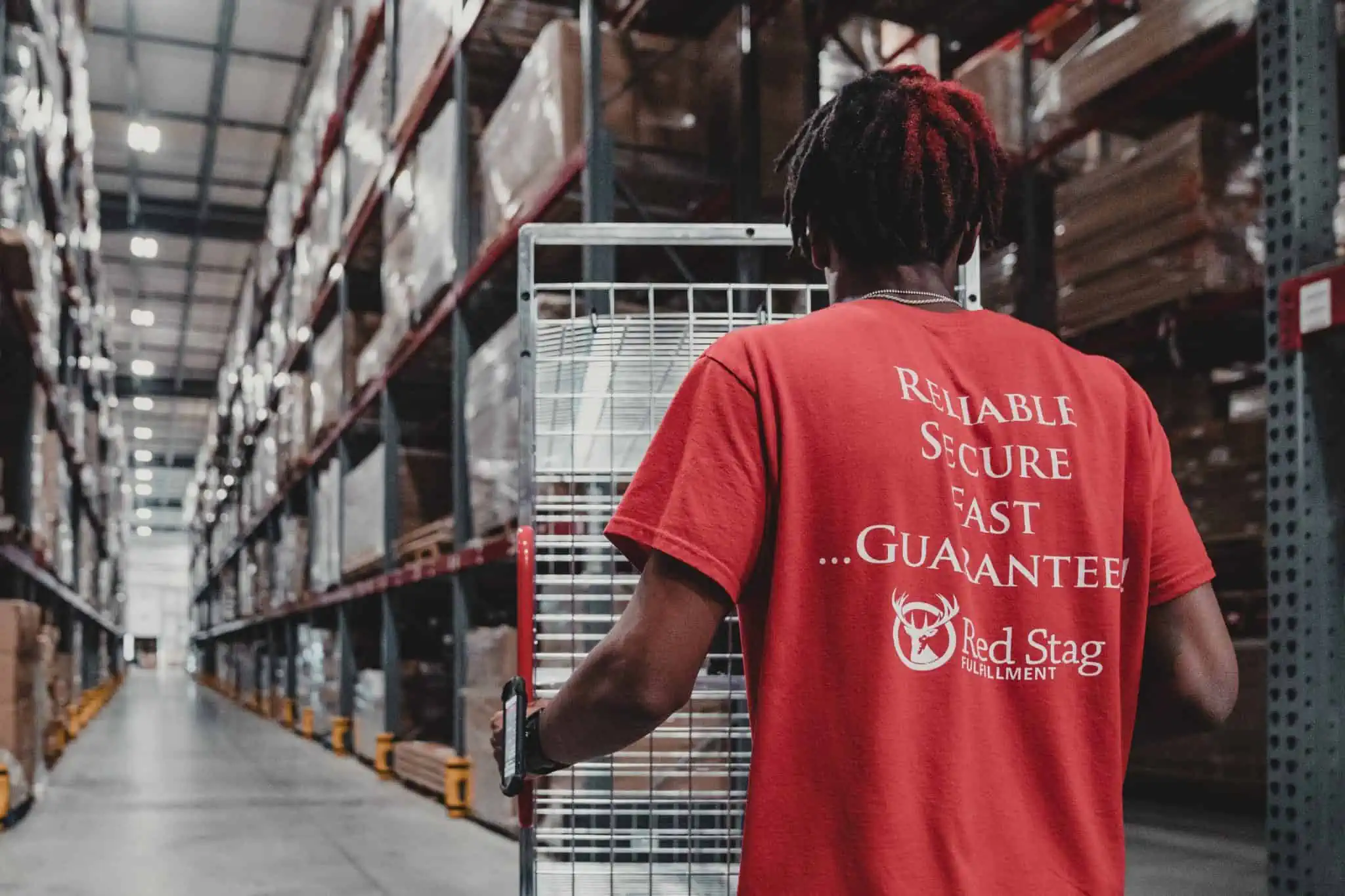
What Are Warehouse Services?
Warehouse services could be simple storage of goods (warehousing). Or companies — like Red Stag Fulfillment — can offer logistics, kitting, and inventory management. Picking, packing, shipping, and storage are each an example of a warehouse service.
It’s crucial to find a warehouse that offers all the warehousing services you need.
What Are The Different Types Of Warehouses?
There are three types of warehouses: fulfillment, storage, and distribution. Many of these facilities don’t fall strictly into only one of these categories.
Fulfillment
A fulfillment warehouse provides third-party logistics services. ECommerce companies ship inventory to the facility. Warehouse services include storage and order fulfillment. Many fulfillment warehouse companies offer additional services such as inventory management and product customization. Logistics warehouses receive products and ship out orders. Most 3PL warehouses serve multiple clients.
Storage
A storage warehouse is primarily for the storage of materials and goods. A government agency might use a storage warehouse to hold seasonal equipment when it’s not needed. A law firm could send old paper files to a storage warehouse for archiving. A storage warehouse may have one client or many.
Distribution
Distribution warehouses receive goods in bulk. A distribution warehouse may be a transfer point in multi-modal transport. Some distribution centers redistribute the products they receive. Grocery chains use regional distribution centers to receive bulk deliveries from suppliers. The distribution center packs assortments of products onto outbound trucks for delivery to individual supermarket locations. A distribution center may service just one company or many.
Red Stag Fulfillment is primarily a fulfillment warehouse, providing expert logistics and warehousing services. We provide inventory storage, so there is overlap in our 3PL facility with other types of warehousing.
See what
our clients have to say
What Are The Primary Warehouse Activities?
Different types of warehouses provide different services. In a 3PL warehouse, the primary warehouse services include receiving, picking and packing, order fulfillment, and shipping. Your warehousing providers should be experts at these core processes.
Receiving
Receiving, or inbound shipping, is the process of checking-in and unloading your items when they arrive by container or tractor-trailer. This is a crucial, often-overlooked, warehouse service. Fast, accurate receiving can mean the difference in having products in stock on your website and ready to sell or unavailable, lost, or on backorder. Once your products have been logged into inventory and placed on the shelves, they are ready for the warehouse team to pick and pack them.
Whether your goods are coming from overseas or across the states, the Red Stag Fulfillment inbound shipping team is ready and waiting to receive and log them as quickly and accurately as possible. You want your products in inventory and ready for picking and packing — and we do, too. That’s why we have accuracy guarantees — like our 2-day dock-to-stock guarantee — and reward our team members for swift, error-free receiving.
Picking & Packing
When your customer places an order on your eCommerce website, the information goes directly to your 3PL warehouse. A picker will find the items for the order, each in a designated space on the shelf. A packer will find the perfect-sized box and add infill around your products so they can ship safely.
Accurate picking and packing is the foundation of a successful eCommerce business. Red Stag Fulfillment was founded by eCommerce entrepreneurs, so our company was built to provide the best fulfillment services in the industry. We pick and pack orders the same day we receive them, with same day shipping available. If we mis-pick or mis-pack an order, we pay you $50. Fortunately, our experienced warehouse staff has a near-perfect accuracy record.
Order Fulfillment & Shipping
The final stage of order fulfillment is shipping. After your order is packed and labeled, it moves to the shipping station. At specific times each day, FedEx, UPS, USPS, and other carriers may stop by the warehouse to pick up outbound shipments. Once a package leaves the warehouse, the carrier is responsible for getting it safely to your customer.
Red Stag Fulfillment services extend beyond the warehouse dock. We have relationships with the major carriers that allow us to negotiate favorable rates and better dimensional weight factors — which can save you money on shipping. And we move heaven and earth to keep your orders going out. In a crunch, when carrier capacity limitations slowed down shipping for other warehouses, we found creative solutions so our clients experienced almost no delivery delays.
Specialized Warehouse Services
Many 3PLs provide specialized warehousing services. These are just a few of the services that Red Stag Fulfillment offers.
Kitting
Kitting and un-kitting products gives you the flexibility to maximize your sales while minimizing your inventory. You can offer both kitted and individual versions of the items. With just-in-time kitting services, your 3PL warehouse can put together the perfect mix you need to fill your orders. Red Stag Fulfillment’s experienced staff can kit and un-kit your products to meet your needs.
Inventory Management
Inventory management is the fine art of having just enough stock on hand, but not too much. A proficient warehousing services company can help you manage your inventory. At Red Stag Fulfillment, we work with our clients to optimize their inventory management based on information that includes sales, seasonality, reorder timing, and other factors.
Cross-Docking
Cross-docking is a method for turning orders around quickly. This process is beneficial for products on backorder. Your warehouse doesn’t waste a day or more putting items on the shelves that will immediately go out again. Red Stag Fulfillment can often turn around a shipment in a day using cross-docking.
Red Stag Fulfillment is primarily a fulfillment warehouse, providing expert logistics and warehousing services. We provide inventory storage, so there is overlap in our 3PL facility with other types of warehousing.
What To Consider When You Choose A Warehouse
When you choose a third-party logistics warehouse for your eCommerce company, you’re making a choice that can have a significant impact on your business. Fast, accurate fulfillment and shipping can win you repeat customers. On the flip side, mis-picks and shipping errors can cost you customer service time and negative reviews.
Here are three things to consider first when you’re deciding which warehouse will ship your products.
Location
When you make a list of attributes you want in your fulfillment warehouse, location might not be at the top of the list. But it should. The location of your warehousing is a big factor in your shipping costs and delivery times. And those make a big difference in customer satisfaction.
Ideally, your logistics warehouse or warehouses should be in strategic, centralized locations. That allows you to offer fast and inexpensive shipping to more of your customers. Unless your business is in a central location, don’t use a warehouse close to your home base. And don’t ship from a port city. Shipping rates increase with every shipping zone an order has to pass through. Shipping costs are highest when you ship from one end of the country to another. Cross-country shipping takes extra time, too. Both factors can lead to lost sales.
Your fulfillment strategy should include one or more warehouses near your customers. That’s why Red Stag Fulfillment has chosen strategic locations for its fulfillment warehouses. If you place your inventory in just two Red Stag Fulfillment warehouses, you can reach 97% of U.S. households in two days or less.
Accuracy
There is nothing more disappointing to a customer than opening a box to find the wrong product inside. Even if you move heaven and earth to fix the error, you can’t erase that first impression. Accurate fulfillment is crucial for the success of your business. Fulfillment errors cost you money in multiple ways: personnel time for customer service, return shipping and reshipping, restocking costs, and canceled orders.
That’s why Red Stag Fulfillment gives every client accuracy guarantees. We will pack and ship each order correctly, or we pay you $50. We’re not in the business of handing out $50 checks. Instead, we keep our accuracy rate as close to perfect as possible. With 99% accurate fulfillment, Red Stag has one of the top accuracy rates in the logistics industry. We aren’t perfect, but we’re pretty darn close.
Speed
Every year, eCommerce speeds up. Customers want their orders delivered quickly. There are two ways to accomplish this. The first is by locating your products in warehouses close to your customers. The second is same-day fulfillment.
Red Stag Fulfillment offers guaranteed same-day fulfillment — your orders are packed and shipped the same day your customer clicks “Buy,” ensuring fast delivery and satisfied customers.
Reach out to start a conversation
Lets find how Red Stag can help your ecommerce business.
Get started by scheduling a quick chat.
Let’s talk