When you finally pull the trigger on your online purchase, you probably monitor your order’s tracking information closely. You wait for those notifications of “shipping label printed” or “leaving UPS facility.” In the excitement of waiting for your new product, it’s easy to forget that each one of those tracking updates has a person behind it making sure your package gets to you safely, accurately, and on time. People like Corey Garrison, Packing Trainer at Red Stag Fulfillment, are the ones making sure that the correct product makes it to your doorstep. In this article, we follow Corey to get an insider’s perspective of a day in the life of a warehouse picker.
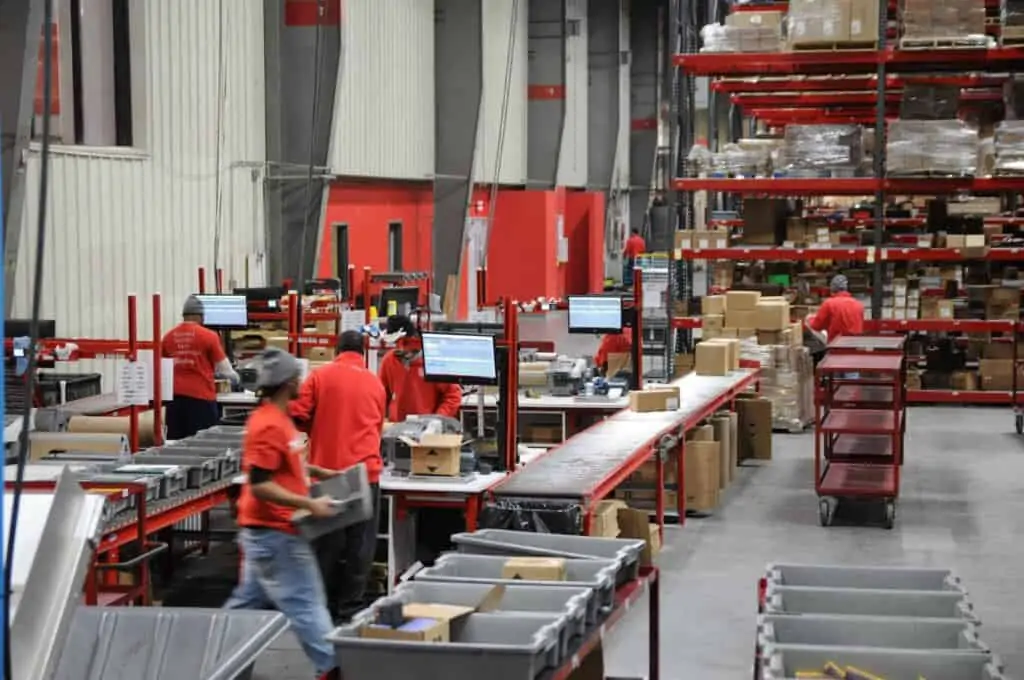
What is warehouse picking?
A warehouse worker takes the packing slip and picks the items for the order from the warehouse shelves. It’s up to the picker to choose the right SKU to ensure you receive the product you’re expecting, so this is an important piece of the fulfillment process. Red Stag’s pickers use a ring scanner to pull customers’ orders and scan for the proper bin location — a process that has built-in redundancies to ensure the correct SKU is scanned into the correct bin every time. Picking sets the pace of the package’s journey within the warehouse and sets the stage for a pleasant unboxing experience in your home.
Stretching it out
On the day we stepped into the life of a warehouse picker and shadowed Corey, his shift began at 8 AM alongside his team members. Similar to any other job, pickers have set schedules they follow to ensure that the orders that have been placed that day are on the truck by 7 pm ET. (Red Stag Fulfillment uses Eastern Time to define the Service Level Agreements we have in place with our clients.)
Once Corey clocks in, he joins a group stretch. “We do stretches in the morning before our shifts — it doesn’t matter which department you’re in. Everyone participates in group stretches before they jump into their shift,” Corey says.
If you aren’t used to the pace of warehouse work, it might sound unusual to do group stretches at your job, but it’s vital for everyone to warm up their muscles and loosen up before the hard work begins.
“Working in a warehouse is a labor-intensive job — it’s hard work and we don’t pretend otherwise. We stretch our neck, back, legs, and arms to make sure we are ready to perform the best we can during our shifts. We don’t want any injuries to happen or someone pulling a muscle,” Corey says as he pulls his batch cart down the aisles of the warehouse.
Shipment and Picking Goals
After stretching, the picking team meets with their team leads to go over announcements, picking goals for the day, and assignments. By doing this, pickers know what to expect and achieve during their shift. On the morning we joined Corey, the picking team already had hundreds of shipments ahead of them.
“We aim to be at zero before 5-5:30 pm, so the products have enough time to be packed and loaded on the last truck,” Corey says. And while hundreds of orders to fill sounds like a big ask, that number can actually grow throughout the day as more orders are placed. At Red Stag Fulfillment, we offer our clients the option of next-day or same-day shipping.
“We take our lunch break at 10:30 am. When we come back, the total number of shipments could increase during that time,” Corey says.
Let’s start picking
Once the pre-shift meeting is done, it’s time to jump into work. Corey gears up with a mobile scanning device that is connected to ShipStream, our warehouse management software (WMS), and his ring scanner to get his day going. Once pickers have their batching cart, their next stop is the picking desk to grab order sheets that contain order information, including barcodes. These sheets will then each be placed into individual bins on the picking cart where the corresponding products will eventually go.
Scanning, scanning, and more scanning
Barcodes on your package and shipping label are scanned multiple times throughout the delivery process. To ensure the correct product goes into the correct bin, the barcode on the sheet as well as the barcode associated with the bin is scanned. By doing this, the information will be logged into the WMS on Corey’s wristband and tracked throughout the picking process. It’s redundancies like these scanning processes that ensure the right product is matched with the right order every time — and it’s one of the reasons Red Stag has a 99.997% accuracy rating.
“If we didn’t have a scanning system, then we would be throwing random products in bins which would cause incorrect orders to be sent to customers,” Corey says.
As Corey scans in the information, the system used within the wristband device will tell him which aisle and shelf location the products will be. The system we use rearranges the product list to ensure an easier and more efficient picking process.
“We pick from back [of the warehouse] to front, so we aren’t just running around,” Corey says. Our system was designed to maintain efficiency and speed in every aspect of the fulfillment process.
Picking the Right Product
Now that the information is logged into the system, it’s time to pick the products off the shelves. As Corey works through the orders in his batch list, he will stop multiple times to check the location numbers on his device.
“Every aisle is labeled a specific way within the warehouse, and each product location has its own barcode,” Corey says as he scans the product’s barcode. “To make sure we are grabbing the right product, we will need to scan the barcode first. The device will notify us if it’s wrong. From here, we grab the product, scan the product’s barcode, and scan the barcode on the bin before placing the product on the cart.”
It can seem like a lot of scanning, but, as mentioned above, it’s these redundant processes that ensure the correct products are picked every time.
Why is efficient, accurate warehouse picking vital?
After one product is scanned and placed in the bin, it’s off to the next item. As Corey moves through the aisles of the warehouse, he is performing a job that is vital for Red Stag Fulfillment.
“You want to make sure you’re getting the right product… Because if you have someone not paying attention when they are grabbing items, it slows us all down ultimately. And in the end, it results in the package not getting to the customer on time — or the wrong product getting to the customer,” Corey says.
With our fulfillment guarantees like order accuracy, we take pride in making sure your customers’ orders get to their doorsteps safe and sound. Red Stag’s questionnaire can help you determine what 3PL services your business needs. If your eCommerce business is looking for a reliable 3PL provider like Red Stag Fulfillment, it might be time to give us a call.