If you have products shipped from your manufacturer to your eCommerce fulfillment warehouse, they will probably arrive in a container. If they come in floor-stacked containers, that can affect your shipping and fulfillment costs.
Here’s the scoop on floor-stacked containers.
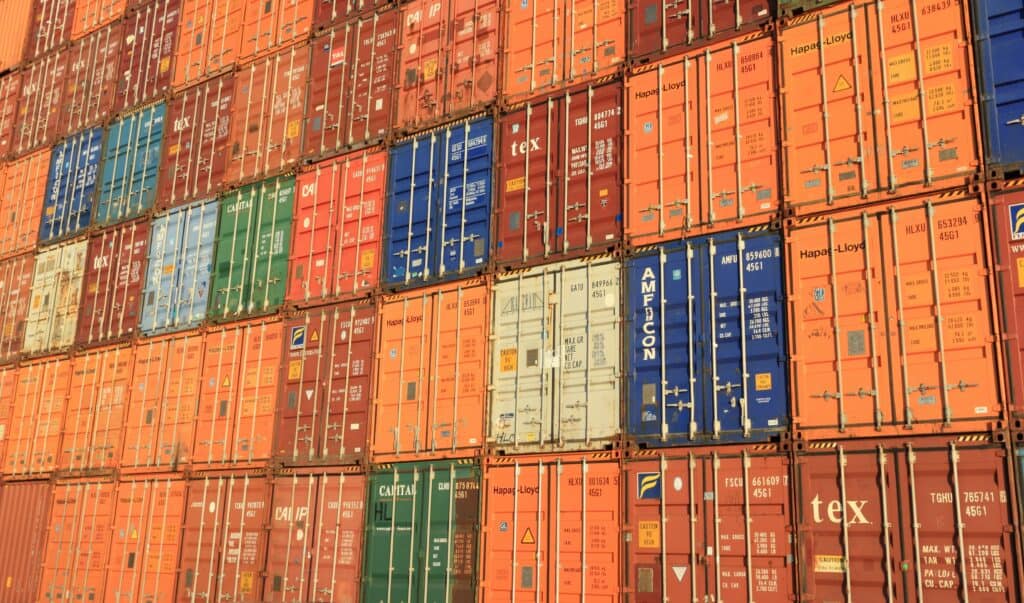
What is a floor-stacked container?
Shipping containers are the basic unit of international and US multi-modal shipment. These enormous steel boxes are stacked into towering piles on container ships that transport products by sea. Once they arrive in port, containers are loaded onto train cars or tractor-trailer trucks for overland freight shipping to distribution or fulfillment centers or other destinations. The standard height of a container is 8 feet, 6 inches; most are either 20 feet or 40 feet long.
Inside a container, cargo can be loaded in different ways. Floor-stacked containers are loaded from the floor to the top of the container with products. By contrast, palletized products are bundled together and strapped or wrapped onto pallets. Floor-stacked containers are also referred to as floor-loaded.
3 problems with floor-loaded shipments
Order fulfillment centers often receive multiple inbound shipping containers every day. Floor-loaded shipments present a few issues during shipping and unloading. Here are three things to watch out for if your products ship in floor-stacked containers.
Protecting products during shipping
Containers go through a lot on their multi-modal journeys. Using pallets to package your products for freight shipping will hold items together and offer some protection from jostling and shifting during shipping. If your products are floor-loaded, you might need to use strapping within the containers to keep things from moving around during transport. Even if your items arrive intact, a dented box may turn a product into a possible reject. Using pallets can ensure that your packaging is protected too.
Another potential hazard of floor-loaded shipments is water damage. Pallets raise your products off the floor of the container, protecting them from water intrusion. If the container takes on water, the bottom of the stack will sit in it.
Floor-stacked shipments require extra services
Floor-loading requires more labor on the outbound side since you need to load each item into the container by hand. On the receiving end, once a floor-stacked container reaches the fulfillment warehouse, unloading also takes longer. Warehouse workers can quickly transport a pallet into the warehouse using a forklift. Most U.S. warehouses operate on a system that is set up to move pallets efficiently.
Floor-stacked containers, on the other hand, must be unloaded by hand, one carton at a time. This can increase the time it takes for new stock to move from the dock and be placed into inventory. Also, because floor-stacking containers require special handling, your 3PL may charge an additional fee to unload them.
Amazon discourages floor-stacked containers
If you use Fulfillment by Amazon (FBA), floor loading can create issues. Amazon prefers products that arrive on pallets and may not process floor-loaded shipments as quickly. Also, you must meet Amazon’s requirements for floor-stacked containers. Otherwise, your shipment could be turned away. If you want to ensure that your Amazon inventory moves smoothly, following instructions to the letter or palletizing are your best options.
Check with your suppliers to know whether they will stack products directly into the container or use pallets to ship your products. Notify your fulfillment company so that it can be prepared. And find out the costs to unload floor-stacked containers.
3 situations where floor loading is the best choice
Floor-stacked containers are advantageous in some circumstances. Here are three reasons you might want to stack your products rather than palletize them.
When every inch counts
Transport can be a costly element of your supply chain. When you ship palletized products, you’re paying for shipping the pallets. In addition, there may be good reasons to use the full capacity of the container. Depending on the origin and destination of a container, floor loading may be the best way to use all the space inside the container for inventory.
Oversized items
Some products are too big to palletize. A large sculpture being shipped from the artist’s studio to the installation location might not fit on a pallet, so a better option is to tether it down inside the shipping container. Also, pallets might not be able to bear the weight of heavy items, such as machinery. If you are shipping products that are too big or heavy to fit on pallets, it makes sense to stack them instead.
Irregularly-shaped products
It’s easy to palletize a block of products in boxes. However, items that aren’t in boxes may not stack well on pallets. Auto and truck tires are both examples of goods that are hard to palletize and sturdy enough to survive transport in floor-stacked containers. Products that are too long to fit on a pallet, such as unmilled timber, segments of pipe, or carpets can travel in floor-stacked containers if they are loaded and secured correctly.
Make your 3PL your partner in streamlining your supply chain
Controlling fulfillment costs is important for your eCommerce profitability. The best way to manage fulfillment costs is to think through every aspect of your supply chain. Your 3PL can help you with that.
At Red Stag Fulfillment, we have unloaded thousands of shipments. We have seen what works and what doesn’t, and we share that expertise with our clients. We want your fulfillment to be cost-effective, accurate, and efficient because that will grow your business, and when your business grows, ours does too.
Red Stag Fulfillment does more than provide storage and ship orders. We work with our clients to optimize inventory management, improve supply chain operations, and reduce dimensional weight charges.
If you need help running the numbers on floor-stacked containers or palletized shipping, give us a call. We’d love to help.