Pallet racking is an essential storage solution for businesses that need to make the most of their warehouse space and efficiently manage their inventory. It’s a system of horizontal beams and vertical upright frames that create a sturdy structure for storing pallets of goods. Pallet racks are widely used in various industries, including manufacturing, distribution, and retail.
When you’re looking to maximize your storage capacity and streamline your operations, a pallet rack system is an ideal solution. It allows you to store products vertically, taking advantage of the full height of your warehouse. This frees up valuable floor space and improves the overall organization of your facility.
Pallet rack systems are highly versatile. With a wide range of configurations and pallet racking accessories available, you can customize your warehouse racking systems to suit your specific needs. Whether you’re dealing with heavy loads, odd-shaped items, or high-volume inventory, there’s a pallet rack system that can meet your requirements.
What is a pallet rack?
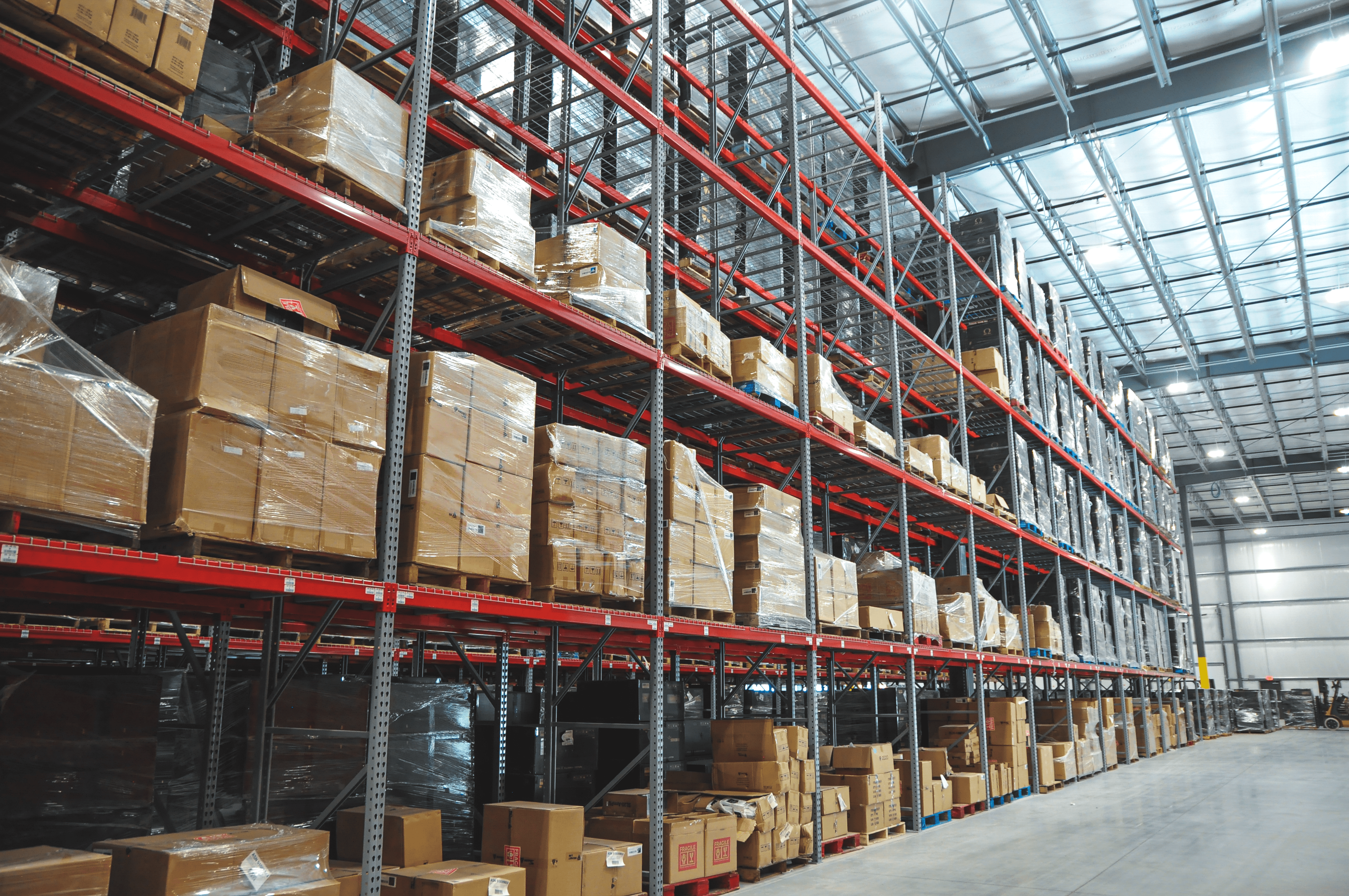
Pallet rack systems are designed to hold palletized materials in horizontal rows with multiple levels. They consist of a series of vertical upright frames and horizontal beams that create a framework for storing pallets. The pallet rack uprights are anchored to the floor and connected by pallet rack beams at various heights, forming a sturdy structure that can support heavy loads.
Warehouse pallet racking helps you maximize the use of vertical space in a warehouse or storage facility. This storage method helps you significantly increase your storage capacity compared to storing goods on the floor. By optimizing your use of storage space, you can store more inventory in a smaller footprint, reducing costs associated with warehouse real estate.
Pallet rack systems are highly customizable, with a variety of configurations available to suit different storage needs. Selective racking, which allows direct access to each pallet, is the most common type. Other variations include drive-in racking, push-back racking, and pallet flow racking, each designed for specific applications and storage requirements.
Benefits of using pallet racks in a warehouse
One of the primary advantages of using pallet racks is the ability to maximize your storage space. By using the vertical space in your warehouse, you can store more products within the same square footage. This increased storage capacity allows you to accommodate a larger inventory without the need for costly warehouse expansion.
Pallet rack systems also offer easy access to inventory, providing a structured and organized approach to storing your goods. With clearly defined storage locations and labeled racks, you can easily locate and access the items you need.
This improved organization streamlines your picking and packing processes, reducing the time and effort required to fulfill orders. As a result, employees spend less time searching for products and fulfill orders faster. This increased productivity allows you to allocate your workforce more effectively and potentially reduce labor expenses.
You’ll also be able to prioritize workplace safety with a pallet rack system. They provide a stable and secure storage environment for your products, reducing the risk of accidents caused by improperly stacked or unstable pallets. They also create clear pathways and reduce clutter on the warehouse floor, further enhancing safety for your employees.
Primary components of a pallet racking system
To fully understand how pallet racks work, it’s essential to familiarize yourself with the key components that make up the system. Here’s a breakdown of the main parts:
- Upright frames are the vertical columns that form the backbone of the racking system. A pallet rack frame is typically made of high-strength steel and is anchored to the floor for stability. The height of the uprights determines the overall height of the racking and the number of storage levels you can achieve.
- Cross beams, also known as load beams, are horizontal supports that connect the upright frames at various levels. Pallet rack beams provide support for the pallets and distribute the weight evenly across the structure. Cross beams are available in different lengths and weight capacities to accommodate various pallet sizes, load weights, and frame depth requirements.
- Decking refers to the horizontal surface on which the pallets rest, and may consist of wire mesh, wooden boards, or metal panels, depending on the specific needs of your storage environment. Decking helps distribute the pallets’ weight evenly, and prevents them from falling between the beams.
- Safety features maintain the integrity of the structure and protect your employees. These features often include the following:
- Locking mechanisms
Pins or clips that secure the beams to the uprights, preventing accidental dislodgment - Pallet supports
Specialized components that prevent pallets from sliding off the racks, such as wire decking or pallet supports - Column protectors
Protective barriers installed around the base of the uprights to prevent damage from forklift collisions - Load capacity labels
Clear labeling indicating the maximum weight capacity of each rack level to prevent overloading
- Locking mechanisms
Different types of pallet racks
When it comes to pallet racks, there are several types to choose from, each designed to cater to specific storage requirements and operational needs. The most common types of pallet racking systems typically include the following five elements.
- Selective pallet racking: A selective pallet racking system is the most widely used type of racking system. It allows direct access to each pallet, making it ideal for warehouses with a high turnover of products. The racks are arranged in a series of single-deep rows, with aisles between them for easy access using forklifts or pallet jacks.
- Double-deep pallet racking: Double-deep pallet racking is similar to selective racking, but instead of single-deep rows, it consists of a two row rack system placed back-to-back. This configuration provide deeper frame depth for greater storage density and reduces the number of aisles required. However, access to the rear pallets is limited, making it more suitable for products with lower turnover rates.
- Push-back pallet racking: Push-back pallet racking is a high-density storage solution that utilizes a series of nested carts. When a pallet is loaded onto the front cart, it pushes the other pallets back, creating space for the next pallet. This type of racking is ideal for storing multiple pallets of the same product because it allows for last-in, first-out (LIFO) inventory management.
- Drive-in/drive-thru pallet racking: Drive-in and drive-thru pallet racking systems are designed for maximum storage density. They consist of deep lanes with rails that support the pallets, allowing forklifts to drive directly into the racking structure. Drive-in racking has a single entry point, while drive-thru racking has entry points on both ends. These systems are best suited for storing large quantities of the same product since access to individual pallets is limited.
- Pallet flow racking: Pallet flow racking, also known as gravity flow racking, is a dynamic storage system that utilizes inclined rails and rollers. Pallets are loaded onto the higher end of the rack and move down the incline using gravity, allowing for first-in, first-out (FIFO) inventory management. This type of racking is ideal for products with a high turnover rate and strict expiration dates, such as perishable goods.
When selecting the right type of pallet racking for your warehouse, consider factors such as product characteristics, inventory turnover, available space, and material handling equipment. By choosing the appropriate racking system, you can add significant efficiency to your inventory storage and fulfillment operations.
How to choose the right type of pallet racking
When choosing the right type of pallet racking for your warehouse, it’s important to first evaluate the size, weight, and shape of the palletized materials you’ll be storing. Some pallet rack frames are better suited for heavy or bulky items, while others are designed for smaller, lighter products. Consider the pallet dimensions and load capacity to make sure the pallet rack system can accommodate your goods safely.
Next, note the frequency at which your products move in and out of the warehouse. If you have high-turnover items that require frequent access, a selective pallet rack system or pallet flow racking system may be the best choice. For products with lower turnover rates, double-deep or drive-in racking can provide higher storage density.
Your warehouse space and equipment are also important considerations. Measure the dimensions of your warehouse and consider the layout and ceiling height to determine the right type and configuration of pallet rack for your business.
If you have limited floor space, consider racking systems that maximize vertical storage, such as drive-in or push-back racking. Some pallet racks require specific equipment for efficient operation, so make sure that you have the right equipment to manage loading and unloading.
It’s also important to consider safety factors such as load capacity, rack stability, and fire safety requirements. Consult with a professional racking provider to help you stay compliant and get the necessary permits.
Of course, before deciding on a pallet rack system, you’ll need to assess the required budget and make sure that you can justify the price tag. Different types of racking come with varying costs, depending on the materials, complexity, and storage capacity. Consider the long-term benefits and return on investment when making your decision.
Getting started with a pallet rack solution
Choosing the right type of pallet racks tailored to your specific needs is crucial for optimizing your operations and achieving long-term benefits. As your business grows and evolves, a modular pallet rack system can adapt to your changing needs, providing the flexibility and scalability required for future expansion.
As you explore your options for developing your own pallet racking system, consider Red Stag Fulfillment for short-term pallet storage. Our experienced team can offer guidance on planning the best pallet rack option for your business, whether that means building your own operation or partnering with our fulfillment team to take advantage of our strategic warehouse locations and customized fulfillment solutions.
Get in touch with our team to learn more about your pallet racking options.