Because people use the terms interchangeably, we often get questions on how distribution centers work and their impact on an eCommerce supply chain. So, let’s take a look at the standard distribution center, its activities, and its role in broader warehouse management.
Defining a distribution center
A distribution center is part of a supply chain network where goods are stored and later sent out to customers or a company’s own locations. These centers move large volumes of products. Their fulfillment targets are often fulfillment centers or large retailers.
Many companies that manage an extensive supply chain will have their own distribution center to manage a region. This company could be a department store chain where goods from many manufacturers are sent to a distribution center. From there, the company uses technology and centers to track store inventory levels and replenish stock on a set schedule.
The distribution center may ship everything from jeans and jewelry to dining room sets and TVs to a local retail location in a single order.
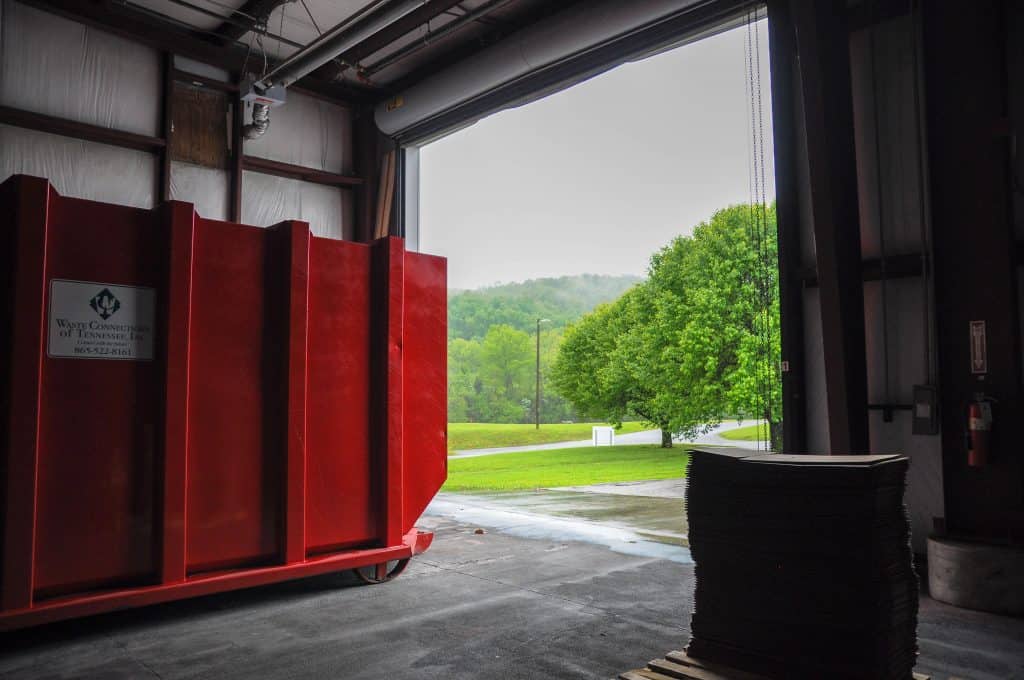
How distribution centers work
Distribution centers can have a broad range of services and departments that you may see in a standard fulfillment center. However, the core difference here is that third-party distribution centers primarily focus on using warehouse storage support to retailers or fulfillment centers. They’re about moving goods in larger quantities than individual end-consumers need.
So, this inventory management will look a little different. To get a handle on that, let’s consider the order fulfillment, logistics, and management processes common to many distribution centers.
Inbound freight
A feature central to how distribution centers work is managing inbound goods, often in the form of large freight shipments. These inbound goods will typically come from manufacturers and wholesalers in LTL and FTL loads that need to be verified and stored.
The size of the inbound freight heading to a distribution center usually means a lot of large equipment is put to use. Forklifts and motorized carts will be common as well as pallet jacks and small trucks. As goods are counted and staged, workers may drive some SKUs to different locations around the distribution center.
When it’s a warehouse distribution center, you can expect teams to monitor SKUs closely and repackage items as needed. Pallet wrapping, moving goods to conveyors, and even combining across shipments to form new pallets are all warehouse actions that you’ll find in a distribution center.
Receiving, putaway, and QA
Order processing can change how distribution centers work significantly. In some cases, they’ll prioritize cross docking, while others will have a fairly standard warehouse receiving and putaway effort.
Think of distribution centers as ways for companies to move many different products at volume to a single location. From there, the warehouse and distribution center teams can move orders in smaller volumes to nearby locations. They might be LTL or FTL loads, or they could be individual trucks.
A grocery store chain may have a local distribution center, for example. In this location, large shipments of cereal and frozen waffles would come to this central location. Teams would receive this inbound inventory, put it on shelves, and eventually, a few units of each SKU would go out together along with loaves of bread, granola bars, and everything else an individual store might need to stock the breakfast aisles.
This department is usually involved with quality assurance (QA) tests as well, unless the distribution center is large enough to have a separate QA team. These warehouse workers will check products, both randomly and periodically, to ensure that everything meets customer requirements. Distribution centers are equipped with the tools needed for each SKU, and customers should drive the process. Most warehouse QA teams will also perform inventory counting across all storage locations to determine shrinkage and potential costs or other issues.
Bulk and breakbulk
Distribution centers tend to have a bulk “department” to handle their largest inbound and receiving steps. These teams in the distribution center will also focus on high-volume goods, where a single client or company will have its own large set of rack space.
The bulk team will unload pallets and cartons or other large combinations of SKUs and units. Then, these are shipped to the appropriate location within the warehouse or storage space.
Ahead of order processing and order fulfillment steps, this department will also manage some breakbulk activities. This generally involves overweight or oversized goods that don’t fit in standard cargo containers. If products were deconstructed for the shipping process — common in ocean freight — then this unit may also reconstruct goods from the various bags, boxes, drums, crates, and other containers that were used to cross the seas on a ship.
Picking, packing, and kitting
Distribution centers feel a lot like warehouses and fulfillment centers when it comes to getting orders ready. They follow the same pick and pack processes and use order management systems to manage inventory use. The differences are all focused on small changes from an eCommerce warehouse distribution setup.
The core difference comes in order size. Unlike your fulfillment center, a distribution center will generally create large orders to send to retail partners. That’ll often mean many different SKUs but fewer destinations per day. Sometimes, a distribution center will fill multiple trucks to go to a single destination, especially for refrigerated trucks to places like grocery stores.
The packing functions focus on pallets and large quantities, meaning they create and use fewer new boxes.
Special services also have their own flavor. Distribution centers are equipped with tools to provide specific kitting services. Sometimes, that is a product’s final assembly or breaking down large containers to create smaller batches to meet customer needs. So, they may be shipping crates of your favorite shampoo in boxes that carry 200 units, while the shopping center customer ends up getting boxes of 20 units.
Kitting also has some other implications at this level of volume. A company may pair its distribution center location with a manufacturing facility to import large quantities of parts. That allows the final assembly to take place on U.S. soil with local workers. Sometimes, that will help a company achieve savings on import duties or achieve other benefits through foreign-trade zone (FTZ) programs.
Outbound freight
Warehouse and distribution centers both perform a lot of outbound shipments. A distribution center is generally more likely to outbound at freight levels and may send these goods to a fulfillment center further down the supply chain.
From a functionality perspective, last-mile transportation is generally the same. Warehouse staff will create orders and work with carriers to move goods to meet customer needs. Like all warehouse fulfillment operations, the customer sets the pace, and technology helps the business keep it.
Export operations
Some distribution centers will be part of an international supply chain, so their warehouse management activities include getting goods ready for export. That requires separate storage space or centers for export order processing and inventory management.
While similar to the bulk department’s activities, export operations focus on getting goods ready for the next leg of their international journey. That covers proper documentation and labeling, plus working with multiple customers and partners to secure proper lanes. Target markets drive the business operations. Logistics is typically about getting freight to its next in-country distribution center with as efficient processes as possible.
How does a fulfillment warehouse and distribution center differ?
While they have many of the same processes and technology, a fulfillment warehouse and distribution center typically have different targets. Fulfillment centers from 3PLs like Red Stag Fulfillment tend to have more potential shipping targets.
We can deliver to your company warehouse in a different state, get products to your retail partners, or send individual parcels to U.S. homes. Inventory levels may differ based on the partner, but core management and the practices in the warehouses are similar.
If you want to know which is right for you, think about your customers. Are you moving goods within your supply chain to a location you own where you’ll sell or fulfillment from directly? Are you shipping packages nationwide to individual customers? Do you only have a small select group of retail partners that you serve?
While fulfillment warehouse and distribution center locations serve different functions, they can work together. If you’ve traditionally sold to businesses, but COVID changed all that, it might be time to think about warehouse management and distribution on a smaller scale. You have an opportunity to go direct-to-consumer (D2C). And, that can be as simple as adding another partner and node to your supply chain.
Adding D2C fulfillment to the supply chain mix
Red Stag Fulfillment works with many companies looking to capitalize on the growing consumer demand in the U.S. National brands once found only in grocers, and department stores are now embracing eCommerce to create direct, profitable relationships with consumers.
If that sounds useful to your bottom line, it’s time to have a quick discussion about your fulfillment. Not only can we help you learn how distribution centers work within a larger supply chain, but you’ll discover ways a 3PL can save on those smaller customer-centric shipments that are gaining steam.