One of the first questions new partners and potential customers ask is: What technology can be used to fulfill orders, and what does Red Stag Fulfillment support?
That can be a long answer because, like most things today, there are multiple options to do any job. And technology seems to power more and more of these alternatives. So, this post will look at 10 different types of technology that can be used to fulfill orders and how they might fit into your own company or a partner’s operations. We’ll discuss:
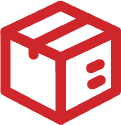
Software platforms
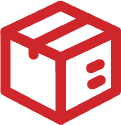
Scanners and tags
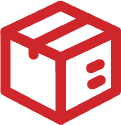
Storage solutions
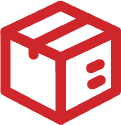
Smartphone and app usage
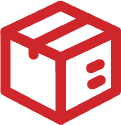
Human-powered carts
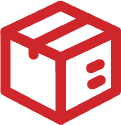
Automated conveyors
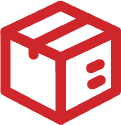
Packing stations
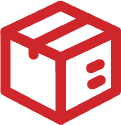
Trucks and vans
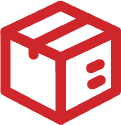
Robotics and future innovations
Order fulfillment covers all the steps a warehouse takes from inventory intake and storage through the final delivery of a complete order to the customer. As we discuss what technology can be used to fulfill orders, we’ll move through the typical steps an order takes from creation to completion.
TL;DR:
Key takeaways
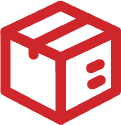
Order fulfillment technology ranges from basic software systems to advanced robotics and drones.
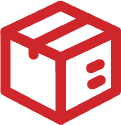
Software platforms (WMS, OMS, ERP) form the backbone of modern fulfillment operations.
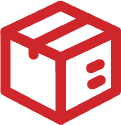
The right mix of technology depends on your product type, volume, and specific fulfillment needs.
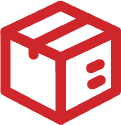
Strategic technology selection can dramatically improve accuracy, efficiency, and customer satisfaction.
10 types of tech used to fulfill orders
Information tools
eCommerce and order software
01
We need to start with the platforms that power orders, inventory, and fulfillment practices for our discussion about what technology can be used to fulfill orders. That means the eCommerce platform is where a sale starts and generates the necessary order information. Typically, your eCommerce tool will handle initial order creation and hand it off to other order or supply chain software, which is where we’ll focus.
There are many different flavors of supply chain and ecommerce software. Some larger platforms, like ERP tools, may include modules that cover the full suite of capabilities that a WMS offers. On the other hand, smaller packages with core functionality are also available for small and growing operations. So you can use a mix to complete your fulfillment.
The explosion of ecommerce has led to more robust platforms and improvements from companies like Shopify. Today’s eCommerce tools can fully manage and track your orders, integrate with warehouse software, and automatically update customers about fulfillment. Your eCommerce platform captures all relevant order details and provides these in a structured way for the warehouse system. That way, pickers get the right products, packers get the correct packaging requirements, and you pick the proper shipping label for the order to be on time.
The alphabet soup of fulfillment software
The fulfillment industry uses many different software types, each with specific capabilities:
• WMS (Warehouse Management System): Manages daily warehouse activities
• OMS (Order Management System): Monitors inventory and order fulfillment
• CRM (Customer Relationship Management): Tracks customer interactions and orders
• SCM (Supply Chain Management): Monitors materials and product movement
• ERP (Enterprise Resource Planning): Large systems for managing global operations
• TMS (Transportation Management System): Supports freight and oversized shipments
So, let’s investigate the alphabet soup of supply chain and fulfillment tech.
Inventory and intake
Scanners and tags
02
Barcodes and tags make warehouse operations significantly easier at every step of fulfillment. They’re essential, from receiving inbound freight and checking inventory levels to picking, packing, and getting something out for delivery. Scanning enables teams to replace manual counts that may miss a box, write down the wrong number, or lose their place due to a distraction.
Barcodes tend to be the default when thinking about labeling technology, which you’ll use to fulfill orders. Not only does every SKU have its own barcode, but you can also apply custom barcodes to pallets, shelves, and equipment. Scanning as something is used generates a wealth of data. Scanning out a forklift, for example, tracks how often your team uses it. That information helps fulfillment professionals keep up with regular maintenance.
Innovations in barcode scanners focus primarily on how scanners move and operate. Like the ones we use at Red Stag Fulfillment, you wear some on the wrist or finger for fast scanning. A conveyor might have multiple scanners to ensure it scans every product moving down a belt. And now, autonomous scanners are moving through aisles to check barcodes and maintain inventory counts to support fulfillment operations.

PRO TIP: RFID (radio-frequency identification) tags can track multiple items simultaneously without direct line of sight. Passive RFID tags are powered by readers, while active tags have their own power source and can transmit data from greater distances, making them ideal for large warehouse inventory tracking.
Storage equipment
03
All that software and tags generate a lot of data. For that information to be helpful, products need an orderly system for storage. That way, it’s easy to ensure you’ve got the right inventory counts and that people or tools know where to go to get each product. Well-defined storage makes a warehouse work. Poor storage increases delays, costs, and customer frustration.
The storage technology most warehouses use will be highly familiar to you. You’ve probably got your own versions within arm’s reach or nearby against a wall. They can also help whether you track inventory individually or by lot. Warehouses customize the exact mix to specific needs. However, some of the most common examples include:
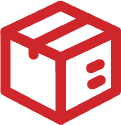
Product storage racks
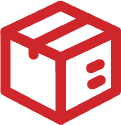
Pallet racks
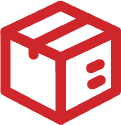
Shelves
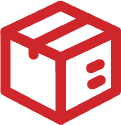
Bins, trays, and custom storage solutions for specialized products
Picking orders
Smartphones and apps
04
In most warehouses, people are still walking around picking up goods for your order. They then bring those to other people at packing stations that prep, pack, and label every order. Then, they or another team stages goods near loading dock doors to speedily put them into trucks for delivery to customers.
That’s a lot of steps where things can go wrong. So, most companies also employ technology to verify that they’ve assembled orders correctly. Some of the newest and most reliable options for what technology can be used to fulfill orders and verify them turns out to be what you’ve got in your hand, pocket, purse, or on the desk next to you: the smartphone.
Many WMS and inventory tools now offer smartphone apps designed to help warehouses and fulfillment operations. The app delivers the pick list. The phone’s camera scans barcodes as the picker gets everything off the shelf. Packing stations also scan products and match them to a specific order. With this, every order is verified and gets the proper label to get to you on time.
In some advanced cases, smartphones and apps will monitor the user’s progress or even offer real-time directions to help someone find a product location.
Carts, hand trucks, and forklifts
05
Pickers have complex, demanding jobs of collecting products all day. Most will turn to a cart or hand truck to put products down as they get everything for an order. They’re standard technology that can be used to fulfill orders, but many differences exist. It’s important to note that you can also use this loading equipment for inbound freight and outbound packages.
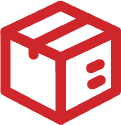
A single-level or multi-level cart that the picker pulls with them.
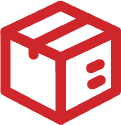
Hand trucks or dollies for stacking heavier goods.
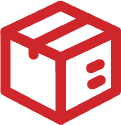
Motorized carts that use sensors to follow the picker automatically, like a warehouse puppy.
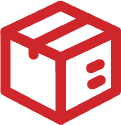
Forklifts and pallet jacks for large or heavy items that need special handling
Conveyors, belts, and rails
06
Larger warehouses use automated systems to store many of their goods. This can be because of the size and weight of products or the sheer volume of goods they manage. Conveyors, belts, and rail systems efficiently move products around a warehouse and help store them in the proper location. Thankfully, many tools also scan and count goods while doing this, helping companies keep an accurate track of their inventory. You can use that data for any advanced inventory audit.
NOTE: A large warehouse can easily have miles of conveyor belts. These systems not only move products but also often include scanners that automatically track items as they move through the fulfillment process. Rail systems, mounted to ceilings or racks, work like “ski lifts for products” and are especially effective for moving palletized goods in high volumes.
Packing and shipping
Printers and packing stations
07
While there are a few fully automated warehouses on the planet, the majority still overwhelmingly rely on people to put products into boxes, tape them up, and get them ready for final order fulfillment. So, when considering what technology can be used to fulfill orders at this stage, think about where the people are.
Warehouse staff who are packing boxes get their own packing stations. These are long tables that are typically left on either side of a conveyor or by the shelving closest to the dock doors. The tables will have nearly everything someone needs to pack an order. Tasks at packing stations include checking to ensure an order is accurate and complete, packing goods inside a box or multiple boxes, adding filler and packing materials, sealing each box, and affixing the proper label.
Key Takeaway: Advanced packing stations typically include:
• Barcode scanners for product verification
• Industrial scales for accurate weight measurement
• Dimension scanners for box size optimization
• Label printers for shipping labels and inserts
• Automated filling systems for package cushioning
• Specialized sealing tools like tape shooters or heat sealers
• Computer systems connected to your WMS for real-time data updates
These stations are designed to maximize accuracy while minimizing packing time and shipping costs through dimensional weight optimization.
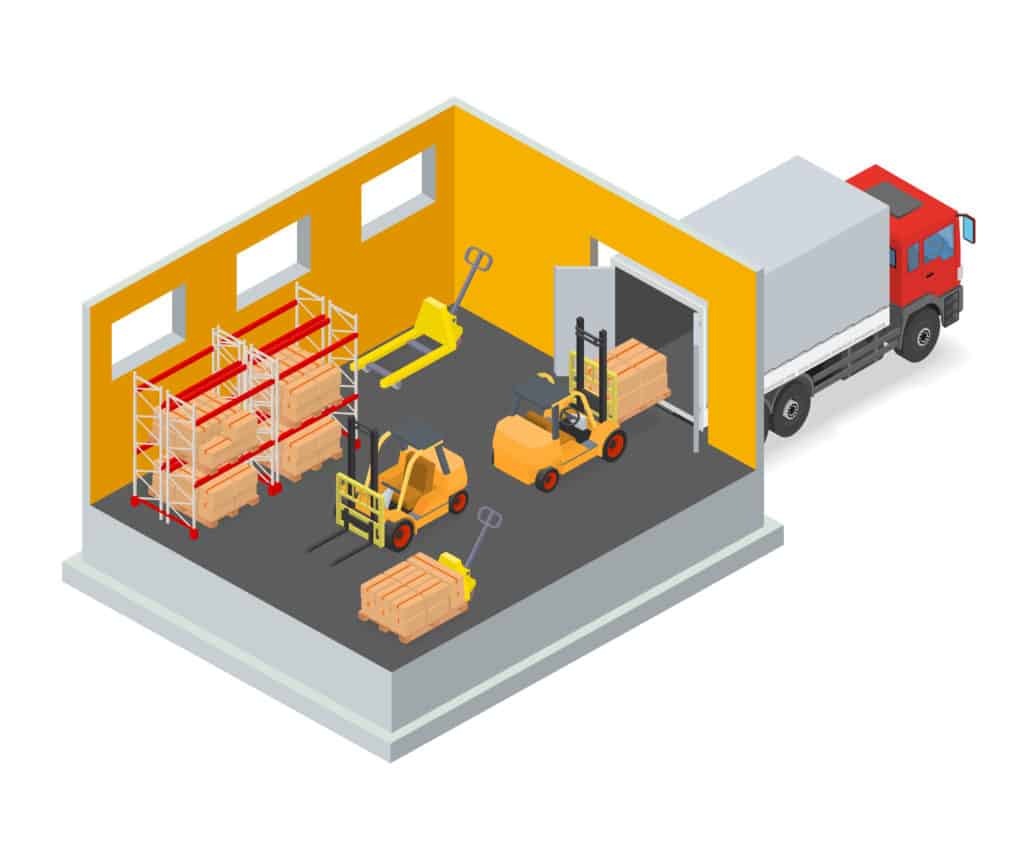
Trucks, vans, trains, and more
08
After an order is packed, it’s put on a cart or sent down a conveyor. Next, they send boxes near the loading dock or area. Most warehouses will continue to use the same order and inventory management platforms and tools at this point, such as ERPs and handheld scanners, as they plan to hand these orders off to carriers.
Order tools can automate pickup requests and schedules with carriers to ensure that you’ve got the right trucks coming to pick up your products. Generally, large and mid-sized warehouses will have trailers backed up to the loading dock to be filled. Orders are scanned and signed for by the carrier’s staff and then proceed to the carrier’s processing facility.
From there, much of fulfillment is out of your hands. Carriers use a mix of trucks, planes, trains, and vans to move goods along each step. Sometimes it can be a single move where a van leaves the processing facility for direct delivery to the consumer. In other cases, packages will move across the U.S. on a truck or train to the next processing facility. From there, deliveries are sent out in those familiar carrier vans.
If you’re expediting orders, a carrier will often use an aircraft for that middle step. In this case, the next processing facility tends to be located close to the airfield used, minimizing travel distance before packages are sorted and set out for final delivery.
Throughout this entire process, carriers scan packages as they move. Modern ERP and order management tools can get this scan data from carriers automatically, updating you and your customers about where a package is. That powers the tracking information we all use regularly, and warehouse systems can be set to monitor this to benchmark carrier efficiency.
What’s next in tech
Robotics and automation
09
One thing to realize when discussing what technology can be used to fulfill orders is that large parts can be automated, and human tasks replaced with robotics. As a result, the warehouse space has seen a boom of robotics, some of which were obvious and others that would’ve been hard to imagine just a few years ago.
Some ecommerce marketplaces that provide their own fulfillment use automated sorting equipment that scans products on a conveyor and automatically routes them to the correct bin via a series of movable belts, robotic arms, and adjustable bins or shelves. Similar systems can move orders from picking locations down to packing stations and send the correct set of bins or products to the right station to complete an order.
NOTE: Much of warehouse automation depends on computerized routing systems that are part of WMS and ERP platforms. These systems must be intelligent enough to efficiently assign orders to available picking stations while avoiding bottlenecks. This requires significant investment not just in robotics and sensors but also in the computing power needed to process the precise data required for smooth warehouse operations.
Automation is a significant investment because of the robotics and sensors, plus the computing power to gather and use the precise data needed to run a warehouse.
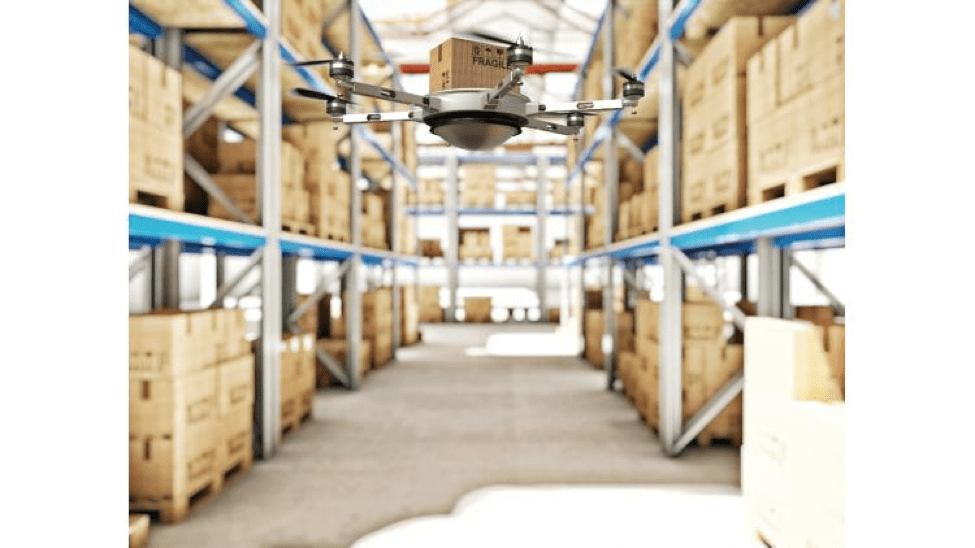
Drones in the warehouse
10
The latest tech to be considered for the warehouse is drones. Many companies first used drones for aerial photography or to take a video of pickers in action. However, drones are now being considered for other use cases. As you may know, drones are a subset of robotics. We wanted to cover them separately because flying changes how they move and navigate around a warehouse.
Today, there are drones available to check barcodes or collect RFID information for regular inventory counts. These systems can be operated by a person or automated and will often fly around a warehouse to scan barcodes and RFID tags after pick-and-pack operations end to update inventory counts. Not only do they create totals, but some gather location data. The WMS or other tools get a full count and can create alerts for any item that’s out of place.
PRO TIP: While inventory-counting drones have been in warehouse testing since at least 2016 (with early adoption by Walmart), their capabilities continue to expand. Some manufacturers are now developing drones that can actually move small bins and goods around a warehouse. Amazon is also pursuing drone delivery for last-mile fulfillment, which could revolutionize home delivery for smaller packages in the coming years.
What technology can be used to fulfill orders for me?
Thanks for sticking with us through all of that. When most partners get to this point, they’ve got one specific follow-up question: What technology can be used to fulfill my orders?
Again, the answer will depend on your sales methods, products, and whether you run your own fulfillment or partner with someone like Red Stag. You probably won’t use everything listed above. We don’t. Red Stag uses many of these tools, and many of the photos in this post are from our warehouses. However, our focus on heavy and bulky product fulfillment takes some tech off the table. Most robotics struggle with large products, and the required upkeep can make them slower and less efficient than having a great team of people.
Key takeaway: The right fulfillment technology mix should be purpose-driven for your specific products and business needs. At Red Stag Fulfillment, we strategically select technologies that enhance our core strengths in handling heavy and bulky items. For example, we use handheld scanners to verify orders multiple times throughout the fulfillment process, helping us achieve one of the best accuracy rates in the industry. The best approach is always one that prioritizes safety, reliability, and accuracy for your specific product types.
So, we use technology for strategic advantages. For example, handheld scanners check orders multiple times throughout fulfillment, allowing us to have one of the best accuracy rates in the business. Forklift experts help us store large quantities of goods efficiently. We chose carts to be the most useful for the size of our products and the aisles in our warehouses. Its purpose-driven.
When considering what technology can be used to fulfill orders, we suggest you take the same purposeful approach. And, like any good partnership, ask questions of the companies where you buy your equipment. In a warehouse, safety, reliability, and accuracy are non-negotiable demands. If you need help or want to learn more, click below to contact us.
What technology do I need for order fulfillment?
For most ecommerce businesses, the essential fulfillment technology includes: a reliable WMS or OMS system, barcode scanning capability, appropriate storage solutions, and packing station equipment. The specific technology mix should be tailored to your product type, order volume, and fulfillment strategy. For specialized needs like heavy/bulky items or high-volume operations, additional technologies like forklifts or conveyor systems may be necessary.
Should I handle my own fulfillment or partner with a 3PL?
When deciding between in-house fulfillment and outsourcing to a 3PL like Red Stag Fulfillment, consider your product specifications, order volume, and growth goals. In-house fulfillment provides more direct control but requires significant technology investment and expertise. 3PL partnerships offer access to advanced fulfillment technology, specialized knowledge, and scalable capacity without the upfront investment. For companies with heavy, bulky, or high-value products, specialty 3PLs with expertise in these areas can provide better accuracy and efficiency than generic solutions.