Every eCommerce business uses pick lists in some form. The type of list and the methods your company uses will depend on the volume of orders you ship and the number of different items you sell. Here’s everything you need to know to use pick lists to improve your eCommerce fulfillment.
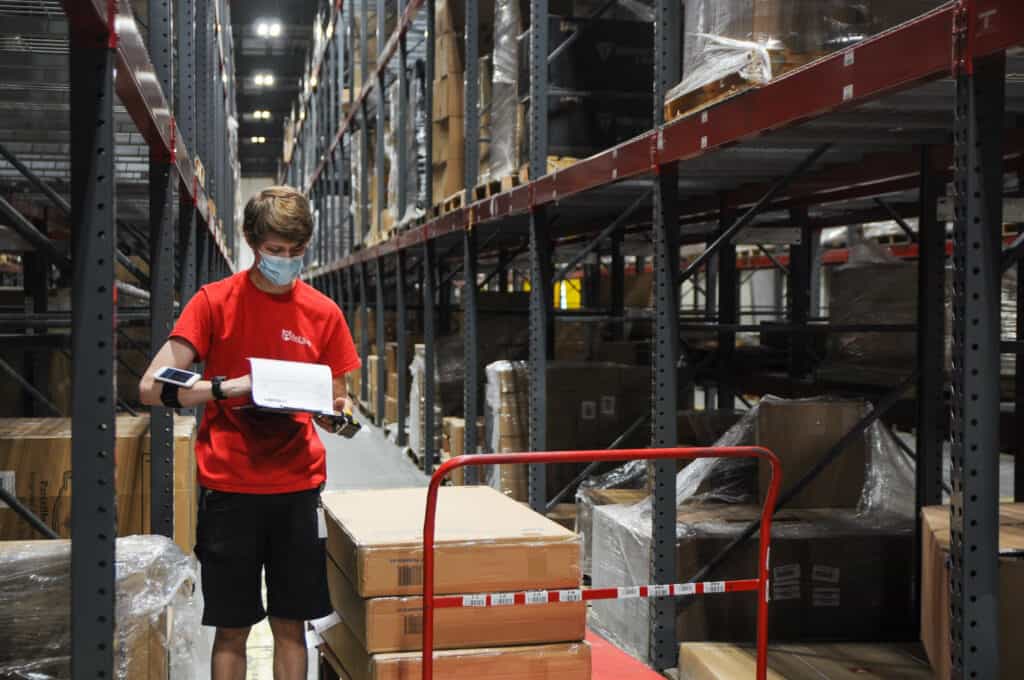
What is a pick list?
A pick list is a document that lists the items needed to fill an order. It may also be called a picking list or pick ticket.
You can generate your pick lists manually or using warehouse management system (WMS) software. A picklist can be as simple as a printed order form. In today’s fulfillment warehouses, however, a pick list is more likely to be electronic. Workers may wear or carry a device that receives order data, creating an electronic picklist. Software is one of the top ways to improve the accuracy of your picking process.
Pick lists help you organize and streamline your order fulfillment. Think of them as a sort of grocery list. When you go to the grocery store, you wouldn’t pick one product from the dairy section, then go to the cereal aisle, then back to dairy. If you’re like most people, you try to get everything you need from each section of the store before you move on rather than ping-ponging back and forth. A pick list allows you to do the same kind of organized “shopping” in your eCommerce warehouse.
When you’re new to eCommerce, picking orders may seem like the last thing you need to consider. You might have a small inventory and perhaps only one SKU, so it doesn’t take much time to fulfill orders without a pick list. However, as your volume of orders grows, so does the value of a well-organized picking operation. Labor accounts for the biggest portion of the cost of warehouse operations. Pick lists and the right pick and pack methods help your staff pick orders more efficiently. That saves money and speeds up order processing.
Best practices for identifying items to be picked
Pick lists are essential because the picking process is where errors in order fulfillment can happen. It’s crucial to clearly identify the items on the pick list, so workers can quickly find the correct items and avoid fulfillment issues.
The order number ensures that items on the pick list are grouped with the correct order. The order number is vital for accuracy, particularly if you have a large volume of orders.
SKU numbers or UPC codes identify the specific product to be picked from your inventory. For products such as clothing that come in different sizes, the SKU will identify the right size for the order.
To speed up the picking process, create a bar code for each SKU (UPC codes already have bar codes). Pickers then use a bar code scanner to ensure they have the exact products on the pick lists. WMS systems are another critical tool as your inventory grows. WMS software can integrate with your bar code system to ensure accurate picking. This system can create an electronic pick list. A good WMS will also allow workers to record their progress through the pick list with the click of a button.
Including a photo of the item can help workers move to the right shelf more quickly. The extra effort to identify products by bar code and images is worth it. You’ll save on labor costs because warehouse staff will be able to move through their pick lists more quickly. You’ll also increase your order accuracy, improve inventory management, and save on returns. And more accurate orders will drive customer satisfaction and sales.
Quantity is an essential element of the pick list, and it’s easy to miss. Make sure your pick tickets display the quantity prominently. Alternatively, use a WMS system that will notify the picker if the quantity is not correct. If your customer ordered multiples of an item, you’ll want to make sure they are all in the box.
Elements of a picking list
A pick list is a list of products that need to be packed and shipped to customers. Your pick list will include some or all of the following information:
- Product descriptions — be specific about the most important characteristics of the product (i.e., size, color, etc.)
- SKU number or UPC codes
- Bar codes
- Images of each item to be picked
- Quantity for each item
- Order number
- Order date
For larger warehouses, your pick list can also include a warehouse location. Creating a system for mapping and numbering aisles and shelves within your warehouse helps workers select each product and fulfill orders more quickly.
Picking methods
There are many different options for picking orders. In some high-tech warehouses, pickers are stationary while robots deliver mobile shelving units to them for picking. Most pickers, however, move through the fulfillment center to search for items to fulfill orders. A pick list is an essential tool in this process.
These are some of the most common picking methods. Choose the option that works best for you based on your sales volume.
Piece picking
Piece picking is where most eCommerce businesses start. With this option, you pick each order as it comes in. In this case, the pick list is usually the same as the packing list that will go into the box. Piece picking is the least efficient picking method. However, it can work perfectly well for small companies.
Batch picking
When your order volume increases, batch picking is a great solution. With this picking method, batches containing multiple related orders are picked at the same time. Each batch is made up of items from the same section of the warehouse. This method minimizes back and forth for the pickers.
Zone picking
The zone picking method is useful in larger fulfillment centers. Each picker works within one zone of the warehouse floor. They search for only the items from their zone on the list. Then they give the pick list to a worker in the next zone to select items for the order.
Wave picking
Wave picking is an efficient method for large warehouses that handle high order volumes. It synthesizes zone and batch picking methods. A worker picks a batch of items in one zone and then transfers the batch to the next zone. The pick list will identify all the items needed from that zone, plus the next zone, for the orders. Batches of orders move in a wave through the zones of the warehouse to the packing station.
How to use pick lists in the fulfillment process
Picking, packing, and shipping are the three basic components of fulfillment. A pick list will make it easier, faster, and more accurate to fulfill orders. Your pick list system is integrally connected to your warehouse organization system. You should create pick lists that guide your workers through the warehouse efficiently.
There are several ways to create pick lists for your orders. You might start by simply printing out each order as it comes in and picking from that, using the piece method. Or you can use a simple tool such as a spreadsheet to organize your picklists. As your eCommerce business grows, you’ll want to adopt a WMS system that generates the pick lists you need to fill orders.
Setting up a pick list system is a great way to improve your operations. But it’s not enough. It’s vital to add robust procedures for every element of your fulfillment process.
Red Stag Fulfillment focuses on quality control in the pick and pack process
One way to immediately improve your pick and pack processes is to outsource your fulfillment to a 3PL. Red Stag Fulfillment employs professionals who bring years of experience in picking orders accurately. We have set up warehouse systems to support our workers and reduce the possibility of errors in the picking system.
At Red Stag, we use barcoding to identify all the items we store for our clients. We also have barcodes on each shelf unit to identify the location. And we put barcodes on the bins we use for picking products. At each step of the process, the picker scans the barcode. Our WMS system flashes back an alert if someone picks the wrong product or puts an item in the bin for the wrong order. We achieve a near-perfect record of accurate pick, pack, and ship services through these checks and double-checks on each pick list.