Pick and pack is the heart of the eCommerce fulfillment process. The picker takes pick lists to the warehouse floor and pulls the products to fill the orders. The packer boxes those items and prepares them for shipping. The pick to box approach combines picking and packing, eliminating the need for packing stations.
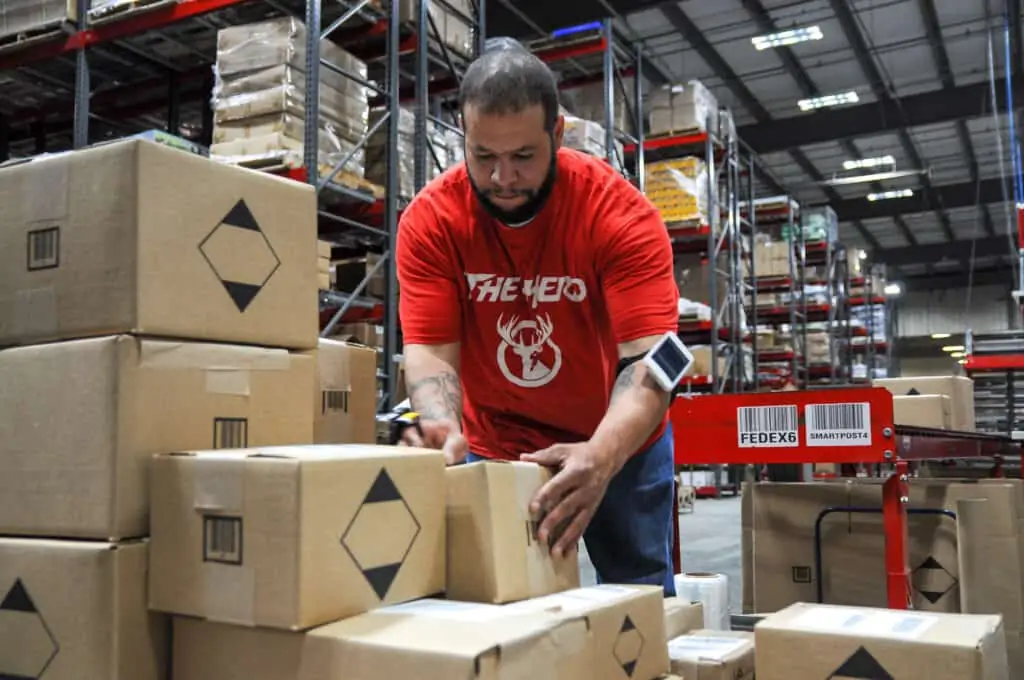
Picking is the most labor- and time-intensive element of order fulfillment. The picker often walks large distances in the warehouse to gather items to fill orders. Though some picking methods aim to reduce the area each picker covers, additional efficiencies can increase fulfillment center output.
Pick to box is just one of several order picking methods, and warehouses often combine it with other picking strategies.
Types of order picking
There is no right or wrong with order picking methods, and each one is suited for specific warehouse layouts and operations. These standard picking methods are the basics of order picking, and you may use any of these methods with pick to box.
Piece picking method
In piece picking, order pickers fill one order at a time. That allows the picker to focus on a single order, reducing picking errors. The downside of the piece picking method is that it is slow because the picker may need to walk the warehouse’s length repeatedly.
Piece picking works best for small companies with a low volume of orders. Third-party logistics warehouses might use piece picking to fill a rush order or push through the final orders at the end of the day, but most 3PLs won’t use this as their primary picking strategy.
Batch picking method
The batch picking process groups orders with the same items together. Because the orders are batched, the picker can pull multiple orders quickly.
Batch picking and the other methods described below are also called cart picking because the picker takes a cart onto the warehouse floor and puts items for each order into a specific bin.
Batch picking helps order pickers take the most efficient route through the warehouse, making order fulfillment faster and more efficient. However, the picker might still have to walk the length of the warehouse to get the items they need.
Zone picking method
Each picker will work in one specific zone in the warehouse during the zone picking process. In most cases, the picker won’t pull all the items for each order. They will pick the products in their area, then hand the cart off to a picker in the next zone to add more items.
Zone picking reduces the distance that pickers have to walk and creates a sort of picking assembly line. It’s a method that works well in large warehouses.
Wave picking method
The wave picking process puts batch picking and zone picking together. Carts with batched orders pass from zone to zone for picking, sending a wave of orders down the line.
Wave picking combines the like-with-like efficiency of batch picking with the reduced radius of zone picking. Pick to box takes efficiency one step further by adding a packing element.
What is the pick to box method?
Pick to box is a type of cart picking that can be used with any of the picking methods above. Instead of taking a cart with bins onto the floor, the order picker loads a cart with shipping boxes and picks orders directly into the boxes. By the time the picker finishes, the orders only need infill, tape, and the label on the outside. A successful pick to box operation requires special software to alert the pickers to the correct box size for each order.
The role of a warehouse packer
To evaluate the pros and cons of pick to box, we first need to understand the role of the warehouse packer.
The packer works at a packing station. Pickers deliver bins to the packers, who find the correct box, follow packing instructions specific to the product and brand, and add the shipping label. Then the packer places the box on a conveyor belt, which takes it to the outbound dock for sorting and shipping.
Pros and cons of pick to box
Pick to box can be appealing, because it combines the role of order picker and packer, which means that warehouse staff are less specialized and more able to fill in for each other. Also, you may be able to handle fulfillment operations with a smaller staff and downsize the warehouse by eliminating packing stations.
However, this method is a step in the opposite direction from other picking methods. Batch, zone, and wave picking create fulfillment efficiencies by focusing the picker’s efforts on a smaller warehouse area. Introducing a whole new task for the picker (selecting the correct box) adds complexity, which can slow down the process and introduce opportunities for errors.
In addition, keeping picking and packing separate adds a layer of process review and expertise to fulfillment. The packer can track which box and infill is appropriate for each order. It may be harder for order pickers to excel at their role if they are tasked with too many different requirements.
Pick to box may be a good option for small eCommerce fulfillment operations and in-house fulfillment warehouses. In a small operation, workers are accustomed to wearing a lot of hats, and this strategy can make the picking and packing process more efficient.
Professional pick and pack fulfillment: the Red Stag Fulfillment difference
Red Stag Fulfillment can meet our accuracy guarantees because we have developed order picking and packing methods that keep our error rates low. Here are just some of the steps we take during the picking process to ensure order accuracy:
- Our pickers use scanners during order picking. They use the scanner to link each order to the code on the bin that order will be picked into.
- The picker scans each item to the order and the bin. If the order picker makes a mistake, the system alerts and stops them until they find and fix the error.
- Our packers don’t just fill boxes — they compare the pick list to the items in the bin before each order gets packaged.
In addition, we offer bonuses to our staff for error-free order processing, and we continuously look for ways to improve our operations. Our commitment is to deliver terrific fulfillment with same-day order picking and shipping.
So, we just told you all about the pick to box method, but we think you should leave that to us. We promise to treat your orders with as much care as if they were our own. If you’re ready for order fulfillment so good that you don’t have to think about order fulfillment, we’d love to talk with you.
More about pick and pack fulfillment:
- What Is Pick and Pack? Improving Your Warehouse Processes
- The Importance of Warehouse and Inventory Management
- The Mis-Pick Effect: Threats Persist