Exceptional warehouse and inventory management are critical elements for a prosperous eCommerce business. Topline metrics like conversions, sales, and revenue aren’t the only measure of online sales success. The movement of products through your warehouse is equally critical to the health and growth of your business.
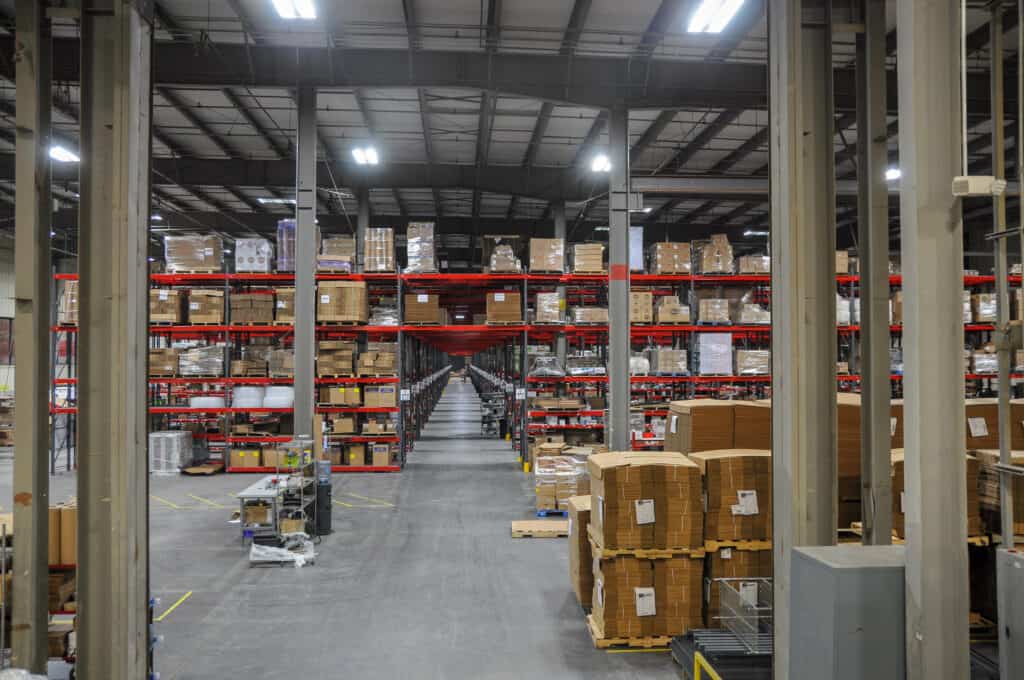
Fortunately, when you use a third-party logistics company for eCommerce fulfillment, you get the help of a team of pros to boost your warehouse and inventory management. But, even if you outsource your fulfillment, it’s critical to understand the basics.
What’s the difference between warehouse and inventory management?
Warehouse management and inventory management are not the same, though they overlap. Inventory management is a narrow set of processes relating to stock. On the other hand, warehouse management encompasses a set of warehouse functions, including inventory management.
What is inventory management?
Inventory management is any process that helps you better manage the flow of products into your fulfillment warehouses. The goal of inventory management is to optimize your inventory levels so you have enough merchandise to fill every order but don’t tie up your cash flow with products that sit on the shelf for long periods.
Inventory management includes:
- Inventory forecasting
- Demand planning
- Setting safety stock and reorder inventory levels
- Tracking inventory through manual inventory counts, spot-check inventories, and other methods
- Developing a process to deal with backorders
Your inventory controls should involve your whole supply chain. Materials suppliers, manufacturers, and transport operators are essential partners in ensuring that you have the stock you need when you need it.
What is warehouse management?
Warehouse management covers all the processes of the fulfillment warehouse. Most warehouses use a warehouse management system or WMS. The WMS is warehouse management software that provides a dashboard for managing warehouse functions.
Warehouse management includes:
- Receiving inventory: Warehouse management involves scheduling dock time for incoming orders and getting products unloaded and placed on shelves. The speed with which your shipments move from dock to stock determines how quickly your inventory is available to fill customer orders.
- Tracking inventory: Warehouses often use barcoding or RFIDs to track each SKU. Sometimes, a warehouse manager will shift inventory locations to optimize order picking. In addition, the WMS will track the amount of inventory, often to the cubic foot, to generate accurate storage charges. And it can track stock age and turnover to determine long-term storage fees.
- Picking and packing: Pick and pack fulfillment is the process of selecting items from the shelves to fill orders and packing them for shipment. Top-notch warehouse management practices can add speed to the pick and pack process, sometimes shaving days off your order lead time.
- Shipping: Warehouse management for shipping can include getting parcels out for delivery with FedEx, UPS, and USPS and packing bulky items or larger shipments onto pallets to be sent by LTL freight.
- Returns processing: Your warehouse will need a process for logging returns so customers can get refunds.
- Inventory management: Many inventory management tasks fall under warehouse management. That includes manual counts and spot check inventories, plus data to support demand forecasting and inventory planning.
- Reporting: Data from the WMS can help you improve your supply chain and inventory management. For example, turnover and aging information are essential in setting optimal stock levels.
Mitigating the effects of COVID-19 and labor shortages on supply chains
Warehouse management is a complex set of functions that must be managed together. Good warehouse management will keep your order fulfillment is fast and affordable. Improving your warehouse and inventory management is more critical than ever today, as disruptions roil supply chains.
To optimize the supply that you need for your eCommerce business, you need to understand:
- Seasonality of sales
- Demand cycles
- Product life cycles
- Production lead times
- Changes in consumer trends and expectations
Small changes can have significant ripple effects along your supply chain. And massive disruptions — such as lockdowns due to a global pandemic, a container ship blocking a central shipping route, or a critical shortage of the labor needed to move products — can lead to interruptions in supply.
You can’t prevent the next disaster from affecting your supply. Still, you can put warehouse and inventory management policies in place that buffer your business from future unpredictable but inevitable disruptions.
Downsides of just-in-case inventory management
It’s important to note that one strategy many businesses have turned to during this chaotic period is not sustainable in the long run: JIC inventory management. Just-in-case inventory is the supply-side version of panic buying, where businesses order more supply than they would usually keep on hand, to prevent stockouts.
While the just-in-time method to manage inventory is less practical in a time of slow-moving transport systems and factory shutdowns, JIC is not the answer. The downsides of the JIC approach include:
- You could get stuck with outdated merchandise that must be sold at a discount or discarded.
- JIC doesn’t work for perishable items. And even products that don’t have a designated expiration date may become less shiny and new if they sit on the shelf for too long.
- It ties up business funds in stock, leaving less money to spend on business expansion, marketing, or product development.
- The extra stock sitting on warehouse shelves can increase the cost to store inventory. Some warehouses charge an additional fee for items you hold for longer than six months or a year.
JIT inventory management is risky and JIC has many costs. So, what inventory control method should your eCommerce business use to weather current and future supply chain disruptions? The answer isn’t simple and will vary depending on your product. However, this is the perfect time to increase your inventory tracking and reporting. That will give you a clear picture of the flow of goods along your supply chain and through your fulfillment center. Plus, it’s worth spending extra effort on an accurate inventory count, so you know precisely what you have in stock.
4 tips to improve your warehouse inventory management system
Here are four concrete steps you can take to boost your inventory management systems.
1. Use inventory management software for powerful analytics
Inventory management software is a vital asset in your inventory management system. The software can automate inventory tracking as new items arrive and products are sold, plus it can provide detailed reporting to support inventory forecasts. The task of tracking stock and reorder levels for dozens or hundreds of SKUs by hand or in a spreadsheet is too time-consuming to be practical. Inventory software gives you a real-time understanding of what you have in stock that you can use to tailor your promotional strategy and focus your production.
2. Do regular physical spot counts to check inventory accuracy
While software does a terrific job automating inventory functions, there’s no substitute for occasional manual counts. A physical inventory will uncover shrinkage and allow you to recalibrate your inventory software.
3. Reevaluate stock levels often
Your inventory forecast will tell you the sales velocity for each SKU. Manufacturing lead time is the time it takes from placing an order to receiving a new shipment of stock. When you reach the number of units of a SKU that you expect to sell during your manufacturing lead time, it’s time to order more, and that’s your reorder number.
But things can go wrong in manufacturing or transport, or you could have a sudden spike in demand for that product, so you want some extra stock as a buffer. That’s your safety stock.
Reorder and safety stock levels aren’t numbers you set once and forget about them. It’s vital to update them as you get new information or conditions change. Regular stock level adjustments are an excellent way to ensure that you have enough stock on hand — but not too much.
4. Enlist your 3PL to help you improve inventory management
Working with a 3PL is one of the best ways to improve your inventory management. Warehouse employees are fulfillment and storage professionals who work with many different companies. Ask them for input and advice about inventory management.
4 tips to improve your warehouse management system
Like inventory management, your warehouse processes should constantly evolve. No matter how good your warehouse management system is, it can be even better. And other warehouse operations (most notably Amazon) are sure to keep increasing their service levels, so you need a top-notch WMS to keep up.
Evaluate picking methods to optimize fulfillment
There are many different picking methods: wave picking, zone picking, and batch picking, among others. Evaluate the speed of order fulfillment using different picking methods to determine the best option for your warehouse.
Assess product placement regularly
No matter what method your warehouse uses, it’s a best practice to store your most popular items closest to the packing station to optimize picking. Reassess which items belong in these coveted spots and adjust your warehouse layout seasonally or as demand changes to ensure efficient warehouse operations.
Use cross-docking to move orders more quickly
Cross-docking allows you to move products directly from the receiving dock to the shipping dock without placing items on shelves. When you have backorders to process or a high order volume, cross-docking can be an excellent option to speed fulfillment.
Work with a 3PL for professional warehouse management
When you outsource your fulfillment to a 3PL, you get the advantage of experience. A 3PL will use a state-of-the-art WMS because it manages a large volume of goods for many different clients. The 3PL management team is focused solely on improving warehouse operations, and they don’t have to divide their attention among many other tasks, as you do to run your business.
Working with a 3PL lets you wear one less hat as a business owner, plus you benefit from expert fulfillment.
3 ways a 3PL can boost your warehouse and inventory management
You will probably wonder why you waited so long once you start working with an outsourced logistics provider. A 3PL will enhance your eCommerce business in many ways; here are just three.
Reduced shrinkage
Shrinkage can eat away at your profit margins and lead to unexpected stockouts. At Red Stag Fulfillment, we believe that handling products without breaking or losing them is part of our professional fulfillment service. Plus, on the rare occasion that inventory is lost or damaged in one of our warehouses, we pay you the wholesale cost, so you never lose money on shrinkage.
Same-day fulfillment
Fulfillment delays can add several days to your customers’ delivery times. Online shoppers expect fast delivery, and same-day fulfillment makes that possible. At Red Stag Fulfillment, we guarantee same-day shipping.
Accurate order fulfillment
Everyone makes mistakes, but a fulfillment mistake can cost you. You might have the expense of return shipping and replacement shipping. Also, while the damage to customer loyalty and retention is hard to quantify, a disappointing or frustrating experience with an order can turn off consumers.
Red Stag Fulfillment’s commitment to quality means that we have one of the lowest error rates of any U.S. 3PL. And our accuracy guarantees mean that, when we make a mistake, we pay you.
How Red Stag Fulfillment helps eCommerce companies optimize their warehouse and inventory management
Red Stag Fulfillment does the hard work of setting up and running warehouse management systems and inventory control systems every day. Our warehouse workers strive for perfect order fulfillment, and we innovate constantly, working to improve everything from the warehouse floor to the software that powers our inventory management systems.
We’ve seen how outstanding fulfillment can help online businesses grow and scale. We’d love to give you a free trial to show you how we do it.
More about warehouse and inventory management: